Baustelle Beton
Ein Bericht von Daniel Hautmann
Die moderne Zivilisation basiert förmlich auf Beton. Der Baustoff sorgt jedoch für Ressourcenschwund, Flächenversiegelung und riesige CO₂-Emissionen.
Beton bringt die Welt in Form; Zement hält sie zusammen. Indem er Kies und Sand zu Stein erhärten lässt, wird er zum Bindemittel moderner Gesellschaften. Unsere gesamte Infrastruktur bräche ohne das Baumaterial in sich zusammen. Autobahnen, Brücken, Flughäfen, Kläranlagen, Krankenhäuser, Schulen, U-Bahn-Schächte oder Wasserleitungen – alles aus Beton.
Jeden Tag ergießen sich 33 Millionen Tonnen des grauklebrigen Breis über unseren Planeten. Pro Jahr kommen so 12 Milliarden Tonnen zusammen. Geschätzte 300 Milliarden Tonnen hat die Menschheit bislang verbaut. Dazu benötigte es Flüsse voll Wasser, strändeweise Sand und Berge an Zement.
Baubranche auf dem Klimaprüfstand
Und dann ist da noch das Treibhausgas Kohlendioxid: So fallen alleine bei der Zementherstellung jährlich rund drei Milliarden Tonnen Kohlendioxid an, bis zu acht Prozent der weltweiten CO2-Emissionen pro Jahr – rund drei Mal mehr, als alle Flugzeuge der Welt ausstoßen, wie der Londoner Thinktank «Chatham House» in der Studie «Making Concrete Change» 2018 vorrechnete.
Zwar ist das alles mindestens seit den 1990er-Jahren bekannt, doch lange lag der öffentliche Fokus auf Flugzeugen, Autoabgasen oder dem Fleischkonsum. Der Zement- und Bauindustrie war das recht, sie stand im Schatten anderer Miseren. Diese Zeiten sind allerdings längst passé.
Allmählich findet in der Baubranche ein Umdenken statt.
Roland Bechmann ist Vorstand und Partner der Stuttgarter Werner Sobek AG, einer global tätigen Unternehmensgruppe, die seit Jahrzenten auf nachhaltige, ressourcenschonende und recyclinggerechte Bauten setzt. Möglichst wenig Emissionen zu erzeugen gehört zu ihrem Credo. Sein Lieblingsbauwerk nennt sich «NEST» (Next Evolution in Sustainable Building Technologies), ein modulares Forschungs- und Innovationsgebäude, das 2016 auf dem Campus der Eidgenössischen Materialprüfungs- und Forschungsanstalt in Dübendorf bei Zürich eröffnete.
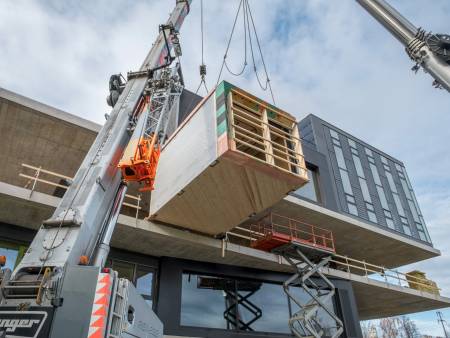
Das einzigartige Gebäude ist Versuchslabor für neue Technologien, Baustoffe und Systeme. «Die verwendeten Materialien werden nicht verbraucht und dann entsorgt; sie sind vielmehr für eine bestimmte Zeit aus einem technischen oder natürlichen Kreislauf entnommen und werden später wieder dorthin zurückgeführt», erklärt Bechmann. Das Gebäude entstand komplett in Modulbauweise: Das Tragwerk aus unbehandeltem Massivholz kann später kompostiert werden. Die Fassade aus sortenreinem Kupfer und Aluminium lässt sich später problemlos recyceln.
Dass es nur wenige solcher zukunftsweisenden Gebäude gibt, liegt auch daran, dass bei Standardbauten Ressourceneffizienz, Emissionen und Recycling bislang kaum eine Rolle spielen. Und es liegt an dem Werkstoff Beton: «Er ist unschlagbar günstig, überall verfügbar, gut zu formen und extrem widerstandsfähig», so Bechmann. «Ein echter Alleskönner. Von der Vielseitigkeit her gibt es nichts Vergleichbares.»
Vom Mörtel zum Stahl- und Transportbeton
Der Betonverbrauch ist, genau wie die Lebenserwartung oder die Kindersterblichkeit, ein Gradmesser für die Fortschrittlichkeit einer Gesellschaft. Den weltweiten Betondurchschnittsverbrauch pro Person beziffert Bechmann auf rund 115 Tonnen. Für jeden Deutschen rechnet er mit 480 Tonnen, die im Laufe eines durchschnittlichen Lebens verbaut werden – schließlich sei uns allen auch ein Stück Bahnhof, Schule oder Schwimmbad zuzuschreiben, erklärt er.
Zentraler Bestandteil des Betons ist neben Sand, Kies, Wasser und zahlreichen Zuschlagstoffen der Zement. Entwickelt wurde er vom englischen Bauunternehmer Joseph Aspdin, der 1824 dafür ein Patent erhielt. Dieser erhitzte ein Gemisch aus Ton und Kalk und erhielt so ein Bindemittel, dass er «Portland cement» nannte – die graue Farbe erinnerte ihn an Kalksteingebilde auf der südenglischen Halbinsel Portland. Den Zusatz «Zement» übernahm er von den Römern, die bereits vor rund 2.000 Jahren mit ihrem «Opus caementicium» kilometerlange Wasserleitungen bauten oder auch Mauern, Hafenanlagen und gigantische Kuppeln, die der Schwerkraft zu trotzen schienen, wie die des Pantheons in Rom. Doch lange vor den Römern, vor 14.000 Jahren, sollen Handwerker im Osten der heutigen Türkei schon Mörtel aus gebranntem Kalk benutzt haben, um Ziegelsteine zu vermauern.
Mitte des 19. Jahrhunderts kam zum Portlandzement eine weitere bahnbrechende Innovation hinzu: Der Stahlbeton wurde erfunden. Stahl gibt dem Beton das, was ihm fehlt – die Zugfestigkeit. In den 1960er-Jahren folgte dann in den USA die nächste Evolutionsstufe: Transportbeton, der, per Betonmischer geliefert, auf der Baustelle direkt verarbeitet werden konnte. Sinnbild sind Wolkenkratzer und Highways, die immer höher – respektive breiter – wurden.
Und während dort die einst in Beton gegossene Infrastruktur bereits wieder zu bröckeln begann, ebnete sie auf der anderen Seite des Pazifiks 700 Millionen Chinesen den Weg in ein modernes Leben – und erreichte neue Rekorde: So habe China allein zwischen 2011 und 2013 mehr betoniert als die Vereinigten Staaten im gesamten 20. Jahrhundert, schreibt Vaclav Smil in seinem Buch «Making the Modern World: Materials and Dematerialization». Bezogen auf die bloße Masse, so der kanadische Umwelthistoriker, sei Zement das wichtigste Material unserer Zivilisation.
«Leichtgewicht» Beton?
Manfred Curbach, Professor für Massivbau und Direktor des Instituts für Massivbau der Technischen Universität Dresden, möchte dem Beton die Schwere nehmen: «Weniger bauen ist ja keine Option, also müssen wir anders bauen.» Curbach setzt dabei statt Stahlarmierung auf eine Bewehrung aus Kohlenstofffaser. Diese Einlage im Beton wäre viel belastbarer und leichter. Das rechne sich, berichtet Curbach: «Mit Carbonbeton kann man mindestens 50 Prozent des Betons einsparen.» Indem die Kräfte von den Carbonfasern abgeleitet werden, ließen sich etwa Deckenelemente deutlich dünner konstruieren.
Zwar seien solche Leichtbaustrukturen minimal teurer und auch die Klimabilanz falle auf den ersten Blick nicht positiv aus, dennoch könne der Einsatz vorteilhaft sein, so Curbach: «Auf die Leistung bezogen ist Carbon schon heute billiger als Stahl; und wenn man statt 400 Kilogramm Stahl nur 14 Kilogramm Carbon verwendet, ist auch die Umweltbilanz besser.» Zudem sei Carbonbeton haltbarer und lasse sich einfacher recyceln.
Der Dresdner Bauingenieur will nicht nur Hightechbauten wie Wolkenkratzer, gigantische Brücken oder spektakuläre Museen mit Carbonbeton errichten, sondern auch ganz gewöhnliche Wohnhäuser. So entsteht auf dem Gelände der TU Dresden gerade das weltweit erste Haus komplett aus Carbonbeton. «CUBE», der 220 Quadratmeter große Experimentalbau, soll 2022 stehen und dem neuen Material den Weg zum Massenmarkt ebnen.
Doch sicherlich wird Carbonbeton allein nicht das Betonproblem lösen. Um in der Baubranche Ressourcenverbrauch und Treibhausgase zu reduzieren, benötigt man eine Vielzahl an Lösungen. Entscheidend wird es zudem sein, dort Alternativen anzubieten, wo neue Infrastrukturen aus dem Boden gestampft werden. Entfallen auf Europa heute nur fünf Prozent des globalen Verbrauchs, wird rund die Hälfte des Betons in Schwellen- und Entwicklungsländern verbaut. Nach China werden Indien und zahlreiche afrikanische Länder ihren Aufstieg «zementieren». Bis zum Jahr 2050 rechnen die Vereinten Nationen mit fast zehn Milliarden Erdenbürgern. 70 Prozent davon werden in Städten leben. Und Beton, ob nun mit Carbonbewehrung oder Stahlarmierung, wird dafür das Fundament bilden.
Balkendiagramm, Pro-Kopf-Verbrauch an Zement, Jahresproduktion pro Einwohner in Kilogramm
Saudi-Arabien, 1.913,
China, 1.713,
Südkorea, 1.146,
Türkei, 954,
Vietnam, 816,
Ägypten, 595,
Deutschland, 410,
Russland, 401,
USA, 265,
Indonesien, 250,
Indien, 202 Kilogramm Zementproduktion pro Einwohner und Jahr,
Baustoff aus Kalk – und Fossilenergie
Kalk, der Grundstoff von Zement, ist für den größten Teil der CO2-Emissionen verantwortlich. Heute werden Ton und Kalk in gigantischen Drehrohröfen bei etwa 1.450 Grad Celsius erhitzt, bis sie zu festen Kugeln, dem sogenanntem Klinker, verschmelzen. Rund die Hälfte des Kohlendioxids entsteht, wenn das im Kalkstein gebundene Kohlendioxid beim Brennen entweicht. Fachleute nennen das «entsäuern».
Der Brennstoff für die Drehrohröfen, meist Kohle oder Öl, zunehmend auch Ersatzstoffe wie alte Reifen, Windradflügel oder Plastikmüll, ist für weitere 35 Prozent verantwortlich. Das Mahlen des Klinkers zu feinem Mehl verursacht weitere zwölf, der Transport des Materials dann die restlichen drei Prozent. Alles in allem entstehen je Tonne Zement rund 800 Kilogramm CO2. Wer weiß, dass weltweit jedes Jahr rund 4,1 Milliarden Tonnen Zement produziert werden, erahnt die Dimensionen.
Doch verglichen mit anderen Branchen hat es die Zementindustrie in Sachen Klimaschutz ungleich schwerer. Während viele Industrien allein mit grünem Strom auf Ökokurs kommen, bleibt ihr dieser Weg versperrt. Was die Welt bräuchte, so Roland Bechmann, sei eine Alternative zum bisher verwendeten Zement – genau genommen eine Alternative zum Kalkgestein. Zwar arbeiten Wissenschaftler bereits an Zementsorten auf Basis von Magnesiumsilikat und anderem Material, etwa am «Karlsruher Institut für Technologie», doch bislang gelingt die Herstellung nur im Labormaßstab. «Ein Durchbruch ist nicht in Sicht», sagt Bechmann.
Perspektiven für «Zement light»
Vielversprechend ist ein Produkt namens «LC3» (Limestone Calcined Clay Cement): Das hat Karen Scrivener von der Eidgenössischen Technischen Hochschule Lausanne (EPFL) zusammen mit Kollegen entwickelt. Ihr Zement ist zwar nicht zu 100 Prozent grün, verursacht aber immerhin rund 30 Prozent weniger CO2. Auch Scrivener verwendet Kalkstein als Ausgangsmaterial, der ist allerdings gemahlen und muss nicht gebrannt werden, setzt demnach auch keine Emissionen frei. Gebrannt wird lediglich der Ton, bei nur 750 Grad – rund der Hälfte dessen, was bei üblichem Zement erforderlich ist. Der benötigte Ton sei weltweit in großen Mengen verfügbar, versichert Scrivener: «LC3-Zement kann mit bestehender Technologie und zu geringeren Kosten hergestellt werden. Er ist daher in großem Maßstab umsetzbar und wird bereits in Kolumbien sowie in der Elfenbeinküste kommerziell hergestellt.» Zudem, so die Wissenschaftlerin, würden weitere Anlagen gebaut, mit dem Ziel, in ein bis zwei Jahren zu produzieren.
LC3-Zement bietet eine realistische Lösung zur Senkung des CO2-Ausstoßes.
Kohlendioxid ließe sich sogar noch viel einfacher einsparen: weniger oder zumindest langlebiger bauen. Immer öfter werden Gebäude bereits nach ein paar Jahrzehnten wieder abgerissen, obwohl sie noch lange stehen könnten. Bei der Internationalen Energieagentur sieht man auch im verantwortungsvollen Einsatz des Baumaterials enormes Einsparpotenzial: Um bis zu 26 Prozent könne man den Zementbedarf reduzieren, indem schlicht nicht mehr in Beton gegossen werde als erforderlich.
Eine weitere Lösung könnte Recycling sein. Sogenannter «R-Beton» enthält bis zu 45 Prozent «Rezyklat», in diesem Fall klein gemahlenen Beton. Das schone zwar Ressourcen, am CO2-Problem ändere es jedoch kaum etwas, schreibt 2019 der WWF Deutschland in seiner Analyse «Klimaschutz in der Beton- und Zementindustrie». Man könnte auch mit Holz oder Lehm bauen. Aber: Lehm ist nicht wasserfest und daher nur bedingt geeignet. Und es gäbe wohl keine Wälder mehr, würde man weltweit alle Gebäude, Brücken, Straßen und U-Bahn-Schächte aus Holz bauen. «Kein Material kann mit Beton mithalten», resümiert Karen Scrivener.
Bauvergaben müssen an strikte Kriterien hinsichtlich der Emissionen gekoppelt werden.
Den Einsatz nachhaltiger Baustoffe behindern oftmals auch die Vorgaben der Behörden – für die stehen Statik und Brandschutz an oberster Stelle, häufig zulasten des Umweltschutzes. «Die Bundesregierung hätte die Möglichkeit, im Baurecht viel mehr zu regulieren und vorzuschreiben. Sie könnte sich ein Beispiel an den Niederlanden nehmen, die bereits einen behördeninternen CO2-Preis für Bauvorhaben haben», sagt die Chemikerin Erika Bellmann, die sich beim WWF Deutschland um den Themenschwerpunkt Klimaschutz in der Industrie kümmert.
Das würde sicherlich helfen, schließlich ist die öffentliche Hand eine der größten Bauherrinnen. Vorbildcharakter habe hier, so Roland Bechmann, etwa Hamburg mit dem Bau der «HafenCity». Dort würden die Grundstücke an jene vergeben, die das beste Gesamtkonzept lieferten, erläutert der Vorstand der Werner Sobek AG und fordert, Bauvergaben an strikte Kriterien hinsichtlich der Emissionen zu koppeln.
Eine globale Branche muss sich wandeln
In Sachen Klimaschutz sei die Betonindustrie auf einem «guten Kurs», schreibt der internationale Branchenverband «Global Cement and Concrete Association» auf seiner Website. Seit 1990 habe man die CO2-Emissionen von zementartigem Material um 19,2 Prozent je Tonne gesenkt – unter anderem durch die Zumischung von Flugasche aus Kohlekraftwerken oder von Schlacke aus Stahlwerken. Doch das kann keine Lösung sein, denn davon gibt es zu wenig. Und dass der Zementverbrauch seit 1990 deutlich gestiegen ist, macht den Erfolg ohnehin wieder zunichte.
Überdies hat der Verband eine «Climate Ambition» verkündet, in der sich die Mitgliedsunternehmen verpflichten, ihren CO2-Fußabdruck zu verringern. Zwar bieten zahlreiche Zementhersteller bereits CO2-reduzierte oder gar CO2-freie Zemente an, «doch die werden bislang kaum nachgefragt», sagt Erika Bellmann. Der Grund? «Die Handhabung, die Möglichkeit von Fehlern und die daraus resultierende Haftung für eventuelle Baumängel ist vermutlich ausschlaggebender als der etwas höhere Preis», vermutet sie. Auch der europäische Handel mit CO2-Zertifikaten könnte besser laufen. Die Zertifikate berechtigen zum Ausstoß von Kohlendioxid und sollen mit der Zeit verknappt werden. Doch: «Die Beton- und Zementindustrie wird in der aktuellen Ausgestaltung als ‹Carbon-Leakage-gefährdet› eingestuft, weshalb sie Emissionszertifikate kostenlos zugeteilt bekommt», bemängelt Bellmann. Man habe schlicht Angst, dass die Industrie aufgrund der mit Klimamaßnahmen verbundenen Kosten abwandert und anderswo produziert und emittiert.
Dekarbonisierung der Zementproduktion
Die Zementgiganten «LafargeHolcim» aus der Schweiz oder «HeidelbergCement» setzen auf eine andere Lösung: das Abscheiden des CO2 im Prozess, «Carbon Capture and Utilization» (CCU) genannt. Kohlendioxid könne auch als wertvoller Grundstoff für andere Produkte dienen, wie etwa für Kunststoffe oder «E-Fuels», heißt es bei Holcim Deutschland. Genau das hat das Projekt «Westküste 100» zum Ziel, an dem auch Holcim mit seinem Zementwerk im schleswig-holsteinischen Lägerdorf beteiligt ist: Hier soll das Kohlendioxid beim Brennen des Klinkers eingefangen und mit grünem Wasserstoff gemischt werden. So will man einen Kerosinersatz gewinnen, mit dem dann die Flugzeuge umweltfreundlicher vom Hamburger Flughafen abheben. «Ein wichtiger Meilenstein auf dem Weg zur Dekarbonisierung der Zementproduktion», sagt Thorsten Hahn, CEO von Holcim Deutschland. Ganz stimmt das allerdings nicht, denn auch beim Verbrennen von Elektro-Kraftstoffen entstehen Emissionen – nur werden sie in dem Fall ausschließlich dem Luftverkehr zugeschlagen.
Beton wird uns – ganz gleich, mit welcher Herstellungs- oder Verarbeitungsweise – noch lange begleiten. Ein Patentrezept für die «Baustelle Beton» gibt es nicht. Politik, Behörden, Industrie, Bauwirtschaft – und nicht zuletzt die einzelnen Bauherren – müssen es gemeinsam anpacken, um den Verbrauch von Beton zu reduzieren und die Zementherstellung zu dekarbonisieren. Dafür werde es, so Leichtbau-Experte Manfred Curbach, nicht die eine Lösung geben: «Wir müssen an vielen Stellen kreativ werden!»
-
Schuld ohne Sühne
Lediglich 20 Unternehmen verantworten 35 Prozent aller CO₂-Emissionen weltweit. Und dennoch ignorieren sie weiterhin alle Aufrufe zur Veränderung.
-
Über den Wolken
Der Flugverkehr ist ein enormes Problem für das Klima. Experten und Organisationen ringen um Lösungen – oder wenigstens um Linderung.